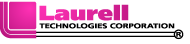
EDC-650 Series
About
This advanced research and development tool is flexible, safe and affordable. The EDC™ series is typically employed for both solvent and aqueous-based processing: Etch-Rinse-Dry, Develop-Rinse-Dry, as well as solvent and aqueous cleaning. The spin processor features a zero-porosity Teflon® fluid path with an onboard dispense valve manifold. A clear ECTFE dome-shaped lid allows safe visibility of your process as it runs, even during single-step process development mode (an exclusive Laurell capability).
The EDC™ system (shown) features programmable valves leading to single injector chemical dispense for repeatability required for Etch, Develop, and Cleaning applications where a rinse (typically DI water or solvent) then dry (typically N2) are the final process steps. With this sequential valving technique, the wafer and plumbing begin and end the process completely dry. Isolated and independent injectors are available in static positions, yet adjustable within the lid. Optional dynamic linear or dynamic radial dispensing is also within the system's attributes. Although a non-vacuum chuck is always recommended for these processes, the system has a vacuum hold-down capability as well.
Features
- Models available for 150 mm, 200 mm and 300 mm wafers and square substrates
- Digital Process Controller
- Solid Natural Polypropylene or Teflon® housing with interlocking clamshell plenum
- Clear ECTFE domed lid
- Teflon® control valves / UD-3b injectors (converts quickly and easily from a pump to a pressure vessel or a syringe)
- Adjustable process N2 diffuser with bowl wash
- Adjustable down-flow exhaust and drain (includes 10' of flexible duct)
- Safety door interlock (disallows rotation and chemical dispense process chamber is open)
- Safety door latch (requires deliberate action to open the process chamber)
- Safety door lock (process chamber can not be opened while a program is running or during chuck rotation after program ends)
Options
- Stainless steel pressure vessels
- ECTFE Halar® encapsulated stainless steel pressure
- Dual containment ECTFE Halar® encapsulated stainless steel pressure vessel (typically for a single a four liter bottle)
- Multiple output injectors
- BP-2 adjustable or fixed rate dispense pump
- English or Metric size non-vacuum wafer chucks
- Small fragment non-vacuum chuck
- Sealed face Vacuum Chucks
- High Porosity Vacuum chucks for thin films and fragile substrates
- Vacuum adapters for fragments as small as 3mm
- Many other chucks are available ... samples or specific size including thickness and ALL tolerances is required
© 2010–2025 Laurell Technologies Corporation