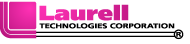
ø150mm Spin Coater
WS-400-6NPPB

See History tab below for more info.
Newer, enhanced replacement model: WS-650-23
Laurell's WS-400 series spin processor, capable of spinning up to ø150mm wafers and 4" × 4" (102mm × 102mm) substrates. 10,000 RPM (based on a ø100 mm SEMI Std. wafer).
Jump to another model:
Available Options
Chucks and Adapters: The WS-400-6NPP comes with a 1.75" (45 mm) diameter vacuum chuck and one fragment adapter. Laurell has many other chucks and adapters to choose from. We can also engineer custom chucks upon request. Details
Liners: Removable, reusable process chamber liners, made from FEP Teflon®, are available for every Spin Coater model.
Manual Syringe Applicators: Available as single or multiple, as well as with Laurell's Edge Bead Remover with adjustable locking positioning. Details
Oil-less Vacuum Pump: A good alternative if a user's facilities do not have adequate CDA or Nitrogen available.
Integrated Variable Pneumatic Vacuum Generator (IV-PVG): Laurell's exclusive hold-down vacuum generator is quiet, inexpensive, and contains no moving parts. Details
Wafer Alignment Tools: Laurell's proprietary wafer alignment tools can be used to effortlessly center wafers on vacuum chucks. Details
WS-400-6NPPB Spin Coater Specifications
Process Controller: The 400-series process controller is capable of storing and automatically running process recipes consisting of run time and acceleration rate, though it can also be run manually.
Housing: The housing for this system is made from a solid co-polymer blend exclusive to Laurell Technologies. Unlike pure Natural Polypropylene, this material is able to resist solvents and strong acids and bases. Samples are available for testing and verification upon request.
Laurell's unique internal bowl design eliminates splash back, making it unnecessary to install "splash rings." Our large down-flow Exhausted Drain Adapter with removable reservoir is as functional as it is convenient. The closed bowl design, coupled with the precision of the process controller, allows most coating materials to dry in a quiescent state, increasing uniformity and minimizing particle contamination.
The upper plenum closes inside the base to provide an overlapping seal, and the inside of the lid has a special gutter to channel fluid to the rear of the system to discourage chemicals from dripping accidentally onto the substrate. This model comes with a 1.75" (45 mm) diameter vacuum chuck and one fragment adapter standard covering 10 mm through 150 mm SEMI wafers. Details
A proprietary labyrinth seal protects the motor and control electronics from chemical contamination. This seal provides the process chamber with Nitrogen purge and has been proven to be particle-free on a sub-micron level during field testing. The system's clear top is made from ECTFE (unless otherwise stated) and only ECTFE-coated 316 stainless steel screws are used in some non-wetted areas throughout the system.
Need more power? Choose a system featuring our 650-series process controller, which uses a more powerful microprocessor and object-oriented program language to achieve nearly unheard of flexibility, both in process definition and use. This controller allows operator interaction in real-time during the process execution, including pausing time, stopping and continuing on from that point.
Researchers worldwide have developed unique processes which will ONLY run with the level of control sophistication we offer. The 650-series controller can also be used in conjunction with a PC using Spin 3000, Laurell's exclusive process management software. However, this is NOT required to program or run the equipment. Note: The 650 is NOT available on 6 series systems.
History
Laurell has decided, after 6,000 units and more than 15 years of production, to only offer the WS-400-6NPP Spin Coater as a manual tabletop system. Since its advent in 1995, it has been the world standard first choice, judged by scientists as the best value. Having continuously through the years exceeded researchers' expectations for reliability and longevity (>90% are still in operation), its replacement was inevitableAugust 2011.
We will certainly continue to produce this model in support of our customers' needs as long as we are able to acquire parts. We will maintain the ability to service the WS-400 for many years, so rest assured, you will always be supported! We are very proud of our achievement and would like to point out to all that the Laurell 400-series Spin Coater was the most successful spin processor of its kind ever produced. The controller has NEVER been equaled and, to this day, remains unique in all the world as the standard for cost, precision and reliability.
The WS-650 controller, which has replaced the WS-400, has been field-proven since being introduced in 2005. With the 650's ability to be upgraded without returning to the factory, our customers will be able to incrementally add items as needed, or take advantage of newly developed capabilities immediately.
Operator and System Safety
Safety: Complete electrical isolation from the operator, fool-proof door interlock, and UL and CSA approval of components assure many years of safe, trouble-free performance. Interlocks prevent rotation when the vacuum switch has not been engaged and when the lid is open. All Laurell systems are CE and RoHS compliant, and all certificates are sent with each system. For more information, please visit the Safety page.
Process Safeguard: The "process safeguard" feature of all Laurell process controllers ensures that the same process cannot inadvertently be run on the same substrate. This feature can easily be bypassed to run the same process again without opening the system or a sequence can be run over an over (looping).
Required Facilities
N2 Process/Seal Purge: 60–70 PSIG (4–5 bar) of Nitrogen/CDA is required to pressurize the labyrinth-type motor seal. This gas also purges the process chamber. The gas consumption is very low, at 3 cubic feet per hour (0.085 m3/hour). 10 feet (300 cm) of 3/16 inch (~4 mm) inside diameter X 1/4 inch (~6 mm) outside diameter PE tubing is provided.
Vacuum: 25–28 inches (~635–711mm) Hg of vacuum with a flow volume of 4.5 SCFM (0.127 cubic meters/minute) at 0 inches Hg is suggested. 10 feet (300 cm) of 3/8 inch (~9.5 mm) outside diameter X 1/4 inch (~6 mm) inside diameter PE tubing is provided.
Power: 95 to 240VAC, 47/63HZ, ~300 Watts
Processes supported
The WS-400 series is typically employed for Solvent, Base or Acid-based processing: Coating, Etching, Developing, Rinsing-Drying and Cleaning. While all of these process are supported, Laurell recommends single-use only, due to known material conflicts. For example, Photoresist and Developer (cross-contamination), and SC-1 & SC-2 (HCl + NH4OH), creating NH4Cl, a hazardous inhalation risk. Dispense options on this model are limited to manual applicators and it is NOT upgradable. For a more capable and upgradable system, see our WS-650 series.
Kudos
© 2010–2025 Laurell Technologies Corporation